Located in one of their plants in India, the sifter is part of their detergent line and the silicon and cloth connectors they had been using were fastened with traditional-style hose clamps that constantly leaked and regularly tore off.
Challenging connector causing major headaches
The detergent-line sifter has a considerable throw of 35mm in each direction, which is very demanding on any flexible connector. The high oscillation caused frequent tearing of the existing connectors and constant vibration throughout the sifter also caused leakage of the powder throughout the surrounding area.
Under these conditions, old-style hose clips tend to rub and cause premature wear on connections, causing tears and regular failures.
The powder leaking into the factory environment was also a health and safety concern for staff. Downtime to repair the failed connectors and the associated labour required to clean up the spilled product was a major issue.
They needed a long-lasting, leak-free solution.
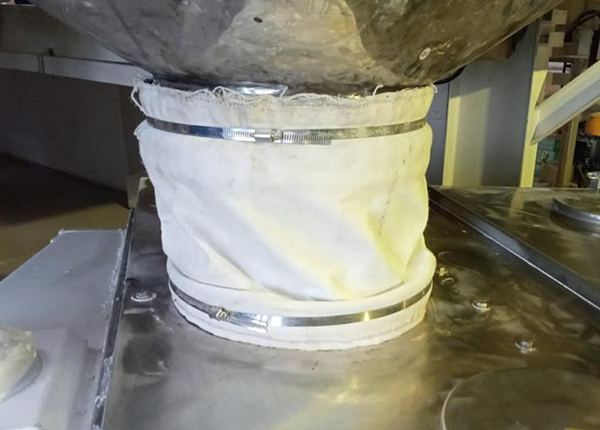
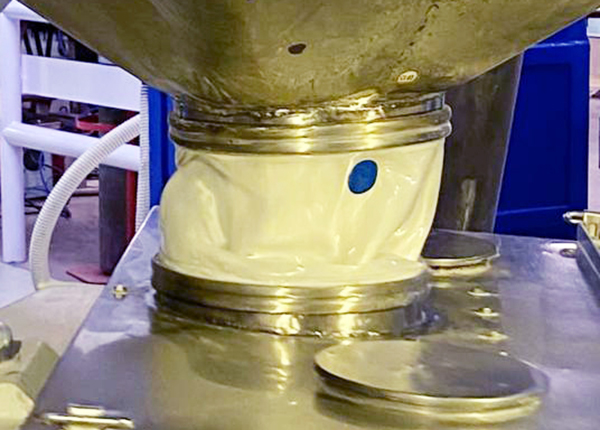
100% sealed and durable BFM® fitting the answer
With the help of local Distributor Airlock India Pvt Ltd, the appropriate measurements were calculated and a BFM® fitting Seeflex 040E flexible connector system was installed on the challenging detergent-line sifter.
The result has been a 100% sealed connection with no leakage at all, despite the large sifter throw involved.
The Seeflex material, exclusive to BFM®, is also manufactured in a way that makes it extremely resilient and durable – it simply won’t tear like most other flexible sleeve products. The snap-fit installation of the distinctive, blue-banded connectors makes it easy for staff to remove, clean and replace when needed, without the need for any tools.
Downtime has been dramatically reduced as there are no longer replacements or clean-up required, and a bonus is that the overall factory environment is also much healthier and safer for staff.
Their production manager was extremely pleased with the result, saying “The BFM® fitting will help us reduce the downtime and increase our productivity. Even though there is a 35mm throw (oscillation) per side, the connector is working perfectly. “
The initial installation has been such a success that the company is now phasing in change-over to BFM® fitting for all their sifter connections in the plant.