Our specialist fabrics are commonly used as the workhorse material within everything from engine hoses, to train gangways and supplied to over 50 countries worldwide.
Now in our seventh decade as a renowned and trusted technical textiles specialist, Arville’s reputation as the go-to provider for textile rubber reinforcement has spread further than ever.
A growing market means Arville fabrics are finding use in an increasingly diverse range of high-performance tires, seals, diaphragms, gaskets, sheeting, and flexible fuel tanks – all of which require an unseen textile matrix imbedded within the rubber.
We weave bespoke reinforcement solutions on our state-of-the-art looms, using high-performance yarns such as high-strength, high-temperature resistant polyesters, nylons, and aramids such as Kevlar®, Conex®, and Nomex®.
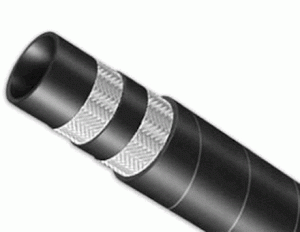
Arville’s technical team is experienced in the weaving of fabrics that are designed for bonding well, accepting rubber matrices, and providing exceptional strength-to-weight/flexibility ratios.
Group Head of Marketing, Andy Smith, commented: “This particular end-use is a growing area of the business for us, driven by developments in material technology and a need from our customers forever lighter, stronger and better-performing materials used in demanding applications.”
Andy continued: “We are well placed to carry on innovating and developing, thanks to our continuous investment plan in new plant and machinery to increase production capacity. Additionally, we are always looking to build on the portfolio of fabrics that we already produce, and welcome fresh challenges from customers old and new.”
As well as flat-woven fabrics, Arville weave tubular fabrics which are cut on a bias angle to allow for improved drape and elasticity when it comes to complex and intricate shapes – this offers customers cost-savings and production efficiencies by eliminating unnecessary wastage in their manufacturing.
Options include finishing treatments with additional bond promoters, to ensure that rubber compounds will key to fibers and process liners for impression-transfer and curing purposes.